Thursday, November 4, 2010
Finished grip tape template
Now that the template is completed I will lay it on the grip tape and cut along the edges with a craft knife.
Template for grip tape
To create the wave pattern I want for my grip tape I had to make a template. I used -----. I drew the design on to the ----, cut it out on the scroll saw and sanded the edges by hand to create a perfectly even finish.
Friday, October 29, 2010
Board painted and varnished
After the varnish has been left to dry for a week it is hard enough to work on the next stage without damaging the surface.
Thursday, October 28, 2010
Grip tape
I have decided to use glow-in-the-dark and black grip tape on my board. I am to place them in a wavy pattern (like the one below) to reflect the underwater theme that I am going for.
The two colours will alternate. To create this pattern effectively I willl have to create a template out of MDF, to ensure that the lines fit together perfectly.
Primer
When the board was sanded to its intended shape it was sprayed with primer (as this board is being). As a safety precaution a gas mask is needed to stop the inhalation of harmful fumes, and it is best to spray in a ----- room.
Sanding
I sanded back the edges to the line I had drawn. I did this on the rounded end of the belt sander to keep the smooth shape of the board. Once this was done I perfected the edges with sandpaper by hand.
Cut out board
I cut the skateboard out, first on the --- saw, and then finished off on the scroll saw. The next step will be to sand the rough edges back.
Thursday, September 23, 2010
Tracing template
I traced the template onto the board, first on one side then flipped it to create a mirror image for the other side. Next week I will cut out the board.
Cutting out template
I cut out my template on the scroll saw, staying approx 10mm form the line the whole way around so that I have room for mistakes and can sand it back the lie perfectly afterwards.
Thursday, August 26, 2010
Creating Template
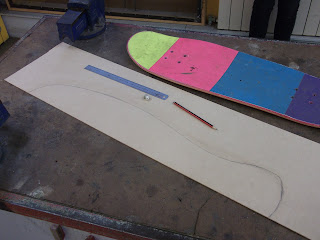
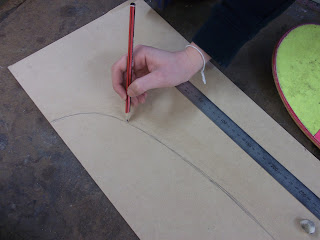
Today we transferred the designs we had created on Freehand onto ply, by hand. We drew half the board so that the template can be used to create a perfectly symmetrical skateboard. We used a finished board to figure out the appropriate length and width, taking into account the kickers at each end. Once this is done the template will be cut out on the scroll saw.
Thursday, August 5, 2010
Back of board
Template Designing
Today we are designing our templates for our decks on Freehand. My design is based on the shape of a short board from the 80's that I really like. It is slightly fish shape so I will probably paint it in accordance with that theme. On freehand I drew the shape of the whole board but when I transfer i to bendy ply I will draw half the design so that when it is traced the deck will become symmetrical. The design will be traced onto bendy ply, which is flexible.
Thursday, July 29, 2010
Brackets on board






We carefully lifted the board and placed the finished skateboard underneath. This was covered in newspaper to protect it. The unfinished board was positioned on top of it. Small blocks of wood were cut out. The unfinished board was bracketed to the skateboard , to bend it to the shape of the original board. Some extra brackets were used to hold the layers of board together while it dried. The small blocks of wood were placed between the brackets and the unfinished board to protect the kauri. The board was left to dry.
Gluing layers


We applied resin to the first on three layers of Fijian kauri. It had to be completely and evenly covered by the resin. This was done by spreading it out with gloved hands, Then we lay down a sheet of fiberglass and pressed it into the resin. Another even coat of resin was applied over the fiberglass and a second layer of kauri was placed on top. This was repeated until the board was composed of three layers of kauri and two layers of fiberglass.
Mixing epoxy resin


Today we had a go at the beginning of the skateboard making process. We started by cutting out four 350mm by 1200mm on the bandsaw. We used Fijian Kauri, which is not a very sustainable wood (see research). We then mixed some Epoxy resin (5 parts resin and 1 part hardener), in the pictures above. We wore latex gloves and surgical masks to protect our skin and lungs from the toxic resin.
Thursday, June 17, 2010
Coloured Resin

Terry has some pigments that we can experiment with next week, so if that works we won't have to buy any.
R180 Epoxy Resin
Nuplex R180 is a modified, low viscosity epoxy resin and is used in conjunction with Nuplex H180 hardener for the construction of reinforced laminates in the Marine environment.
This epoxy system was especially developed for the production of articles where thin film cure is of particular importance. Particular emphasis has been placed on deferral toughness and strength of the cure system. As well as offering high mechanical properties, its low viscosity facilitates wet out of difficult fabrics
Thursday, June 10, 2010
BRIEF
To design and create a skateboard from researched materials. I will make a short deck (retro 80's look) with a kicker (or two) and longboard trucks (the experiment). I need to research what materials will work best and an appropriate shape for the board. When this is done I will design the board on Solidworks and cut it out. Following this I will construct the board, then spray it and attach the trucks.
Subscribe to:
Posts (Atom)